Flare Gas Recovery
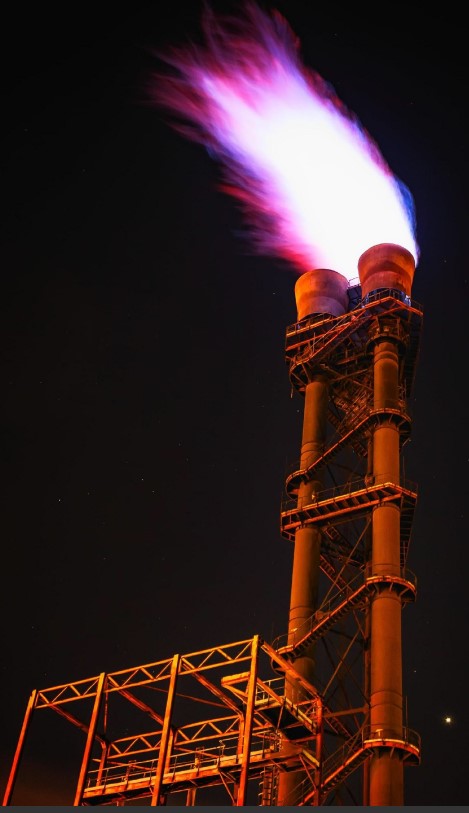
Flare Gas Recovery
Flaring is an unproductive waste of a valuable, non-renewable resource and a significant source of carbon dioxide and methane emissions
To recover the wasted income from flared gas, EAJV offers flare gas recovering technologies to recover valuable resources and reduce the flare gas to achieve near-zero flaring with the methods described below.
1. Processing the flare gas through either water injected screw compressor or liquid ring pump compressor especially designed to handle the flare gases:
The system is especially designed for high hydrogen content gas and a seal water recirculation system. The flare gas is compressed to 8 bar (g) and the heavier hydrocarbons condense out. The collected amine and liquid hydrocarbons enter a gravity separator where the hydrocarbons are decanted off and the collected amine is sent back to process the amine solution. The relatively cleaned flare gas is then sent to a H2S removal system and then to the fuel header. The condensed hydrocarbons are again decanted out and sent to the liquid condensate tank. Upon failure of any component, the flare gas is then passed to the existing flare itself.
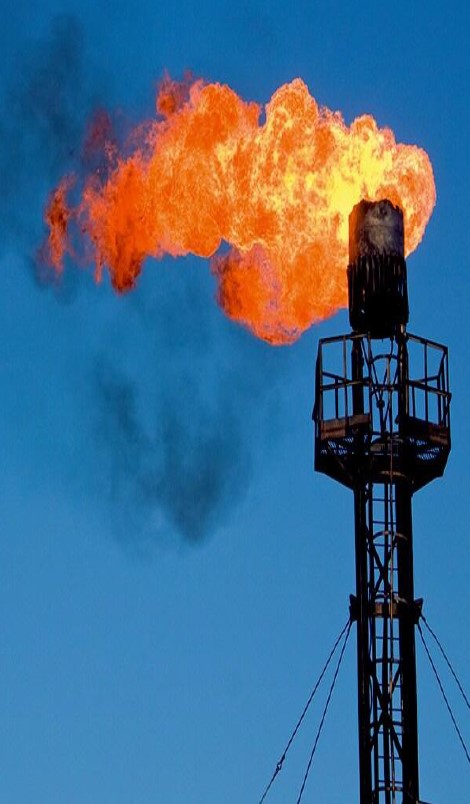
2. Processing the flared gas through a series of educators:
The system is especially designed for flare gas and an amine recirculation system. The flared gas recovery system consists of processing the flare gas through three educator systems complete with all accessories especially designed to handle the flare gases.
The flare gas pressure is increased to 4.5 bar (g) and the heavier hydrocarbons condense out. The amine injection is once through flow system. After leaving the educators, the gas, amine and hydrocarbon mixture enter the Gas/Liquid separator where the compressed gas is separated from the amine and condensed hydrocarbons are separated by gravity due to the lower gas speed. The collected amine and liquid hydrocarbons enter a recirculation tank/separator where the hydrocarbons are decanted off and the collected amine is sent back to process the amine solution. The relatively partially scrubbed and cleaned flare gas is then sent to small tray section tower, where final H2S is removed and then the gas is directed to the fuel header. Upon failure of any component, the flare gas is then passed to the existing flare itself.

3. Processing the recovered and purified flare gas to one of small or medium GTL or LNG plants: to produce either liquid natural gas or liquid fuels that can be transported by truck or rail in the absence of pipelines.

The advantages of EAJV Technology approach are:
- Dramatically reduce flare emissions (Near zero flaring)
- Recover waste gases for fuel, thereby increasing sales gas
- Prolong life of the flare system
- Reduce operating cost
- Improve public perception of operator
- Producing transportable hydrocarbons through GTL or LNG plants