Gtl Technology
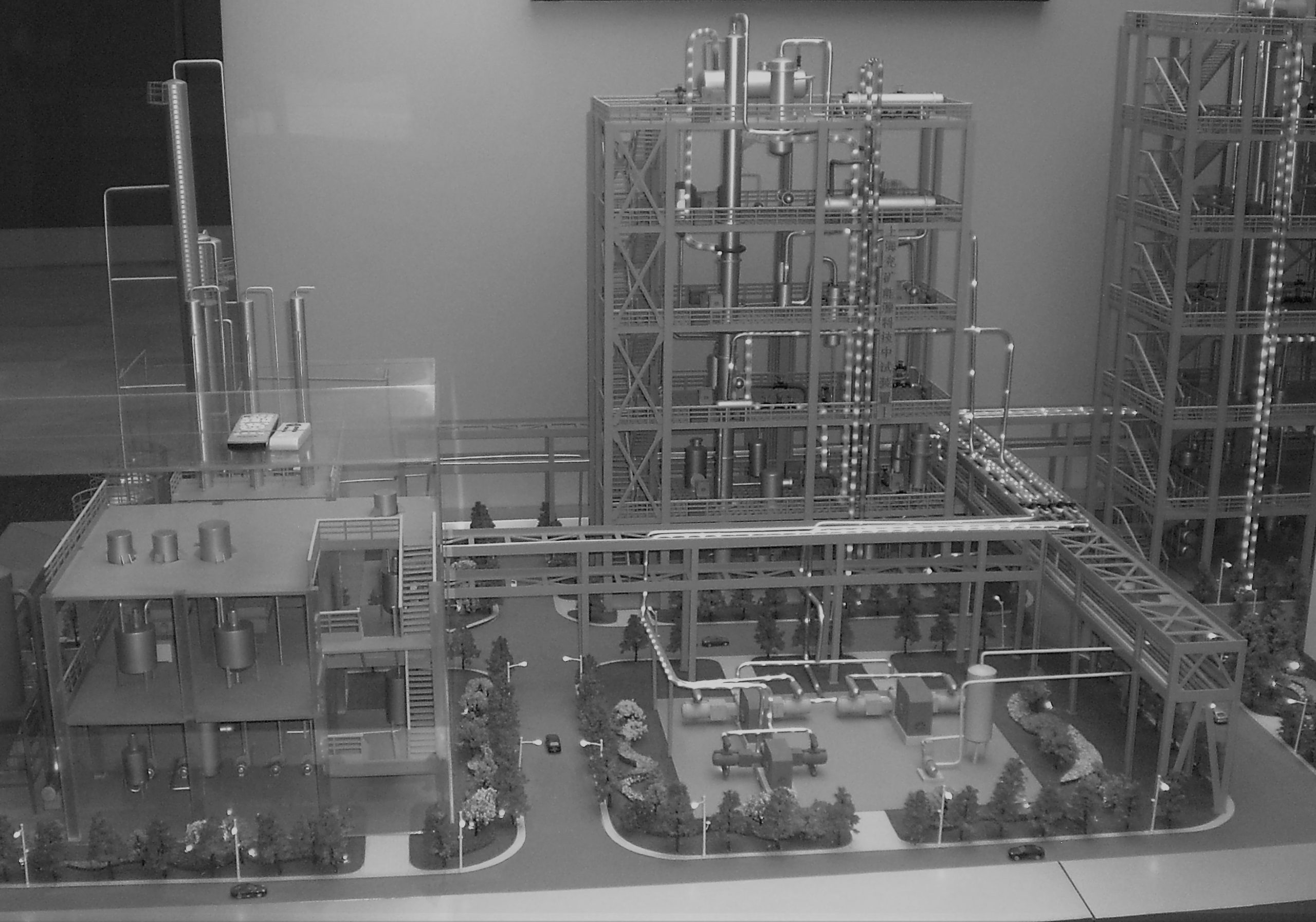
Small GTL A Logical Solution
Historically GTL production has been prohibitively expensive as compared with crude oil refining, however the application of horizontal drilling and fracking has translated, in several parts of the world, into a surge in natural gas production and depressed natural gas prices.
As natural gas feedstock accounts for more than 80% of the cost of GTL products, the technology is now competitive as compared to crude oil refining.
Furthermore, the development of small-size 1,000- to 20,000-barrel per day GTL plants as standardized production units, makes the operation of such plants for stranded natural gas fields a logical and commercially viable solution.
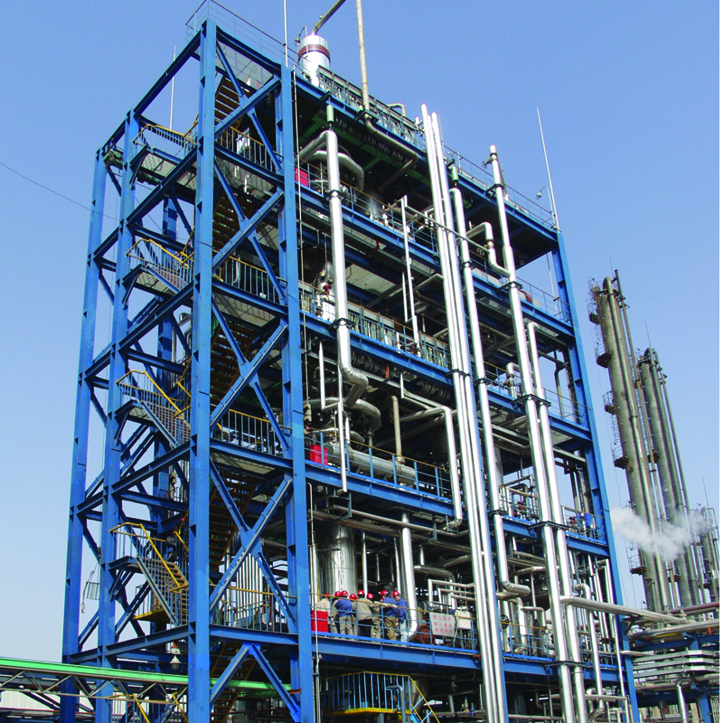
GTL Viability
At today’s natural gas prices, small-size GTL plants are profitable with payback time of 3 years or less. As it is true for chemical plants, the key to the feasibility of a GTL plant is the availability of low cost natural gas for the life span of the plant.
As an example: 1,000 barrel per day GTL plant requires less than 100 billion cubic feet over the 25-year usable plant life.
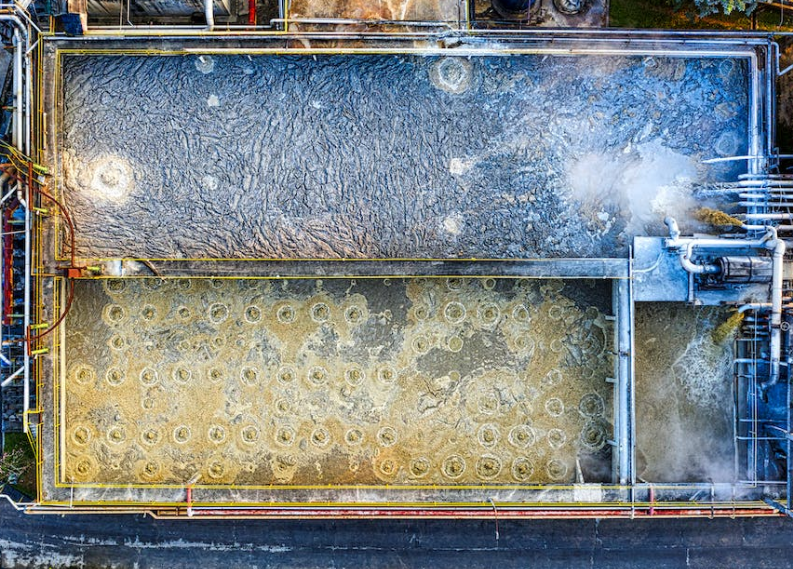
GTL Products
The combustion of GTL fuels produces much lower emissions than conventional fuels, because these GTL products are sulfur, nitrogen and aromatics free.

GTL Diesel
GTL diesel can be used in all conventional diesel engines and is compatible with the existing diesel distribution system. It has very high cetane value and a very low sulfur and aromatics content. These characteristics translate into much lower engine exhaust gas emissions.
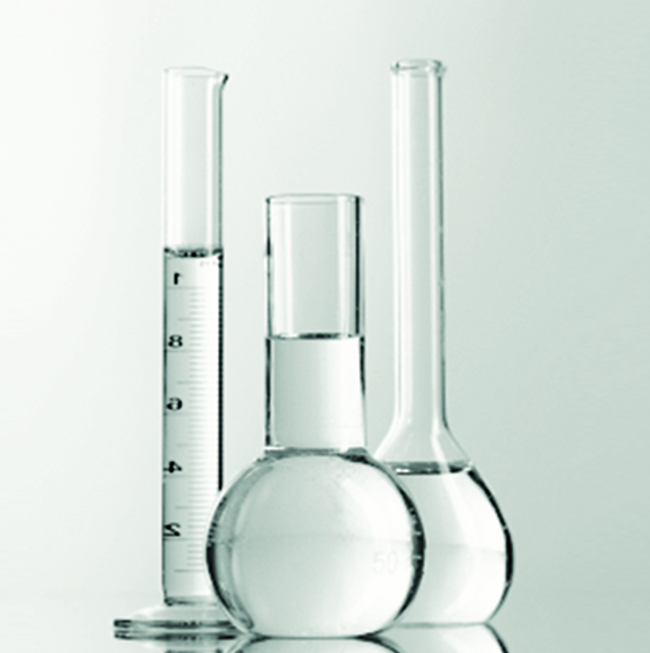
GTL Naphtha
GTL naphtha is almost free of aromatics, sulfur and metallic contaminants. It is almost exclusively paraffinic and has a high normal to iso-paraffin ratio. This makes it an ideal feedstock for ethylene production. Because of low aromatics, cracking GTL naphtha results in reduced coking of furnace tubes allowing longer production runs.
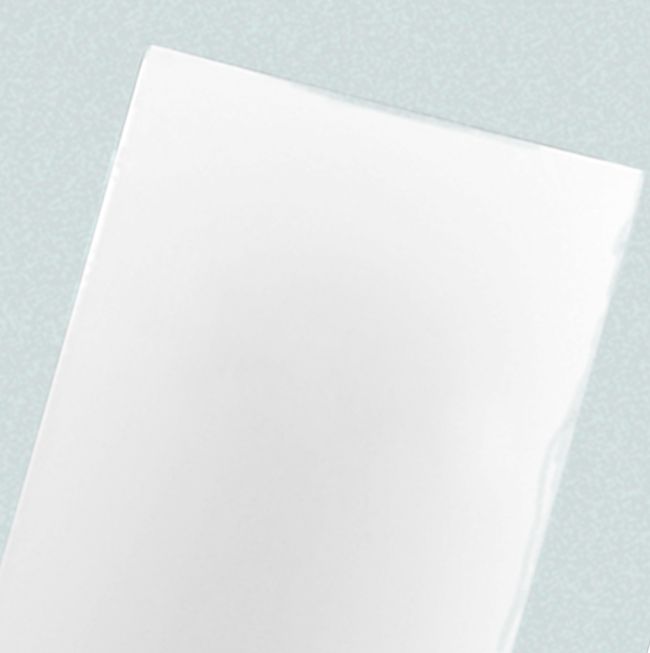
GTL Waxes
GTL waxes known as Fischer-Tropsch waxes, are high purity and high linearity pearl white waxes with melting points from 30°C to 100°C. Synthesized hydrocarbons can be fractionated to different grades waxes with chain lengths up to C100, saturated-linear chains, aromatics, sulfur and nitrogen free.

GTL Kerosene
GTL kerosene can be produced with distillation cut from C6 to C16. GTL kerosene has been approved for use as jet fuel as per the new standard ASTM D7566, in a 50% mixture with standard jet fuel.

GTL Process
The EAJV gas-to-liquids (GTL) process converts natural gas into longer-chain hydrocarbons which are combined into three commercial products: LPG (propane, butane), naphtha and diesel.
After purification of the natural gas into pure methane, the first step of the process is to produce syn-gas, a mixture of carbon monoxide and hydrogen, through partial oxidation in an auto-thermal reformer.
The resulting syn-gas, after adjustment of its carbon monoxide to hydrogen ratio synthetized in a Fischer-Tropsch reactor into a mixture of longer chain hydrocarbons with C3 to C25. The synthesis products are then refined into three or more commercial products including LPG, Naphtha and Diesel
Waxes produced by the synthesis are either commercialized as high grade waxes or cracked into more diesel fuel.

GTL Demonstration
Phase 1 – The low temperature Fischer-Tropsch synthesis reactor is a slurry bed design. The demonstration plant project was started in 2004 and commissioned in 2007.
Phase 2 – Subsequently, a second demonstration plant was built at the same location. This plant has a high temperature Fischer-Tropsch synthesis reactor of the fluidized bed design, and has a maximum production capacity of 700 barrels per day of liquid equivalents. This phase was started in 2008 and commissioned in 2010.
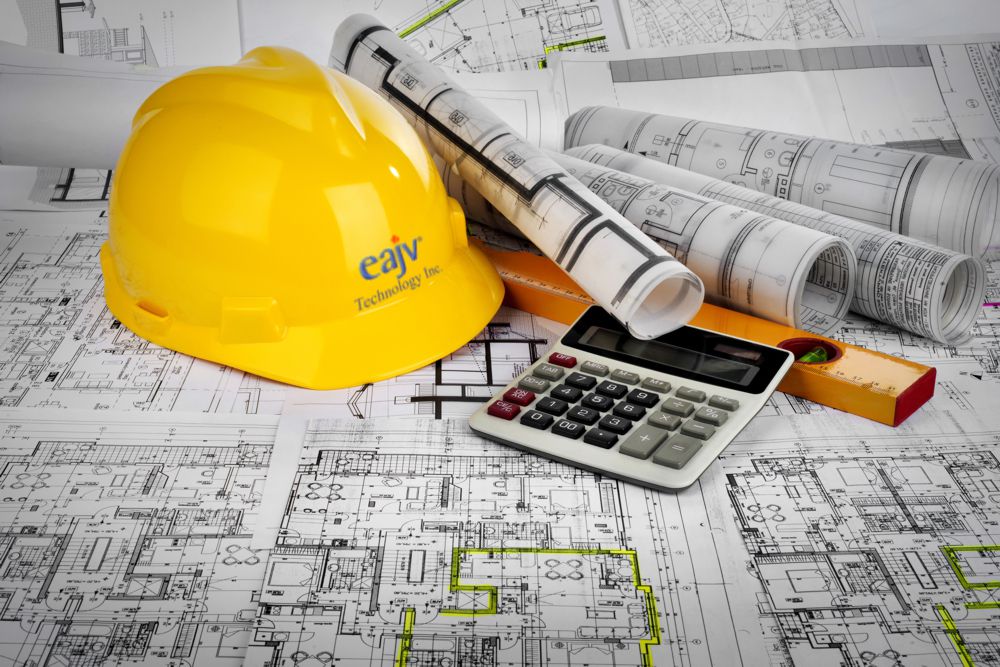
Long Term Technical Assistance
Catalyst and technical assistance are available from EAJV on a long-term contract basis. With this contractual arrangement, the latest advances in GTL technology and catalyst developments are transmitted to the client on a regular basis to ensure that all GTL plants supplied by EAJV Technology benefit from the highest carbon and energy efficiency as well as the highest plant availability.